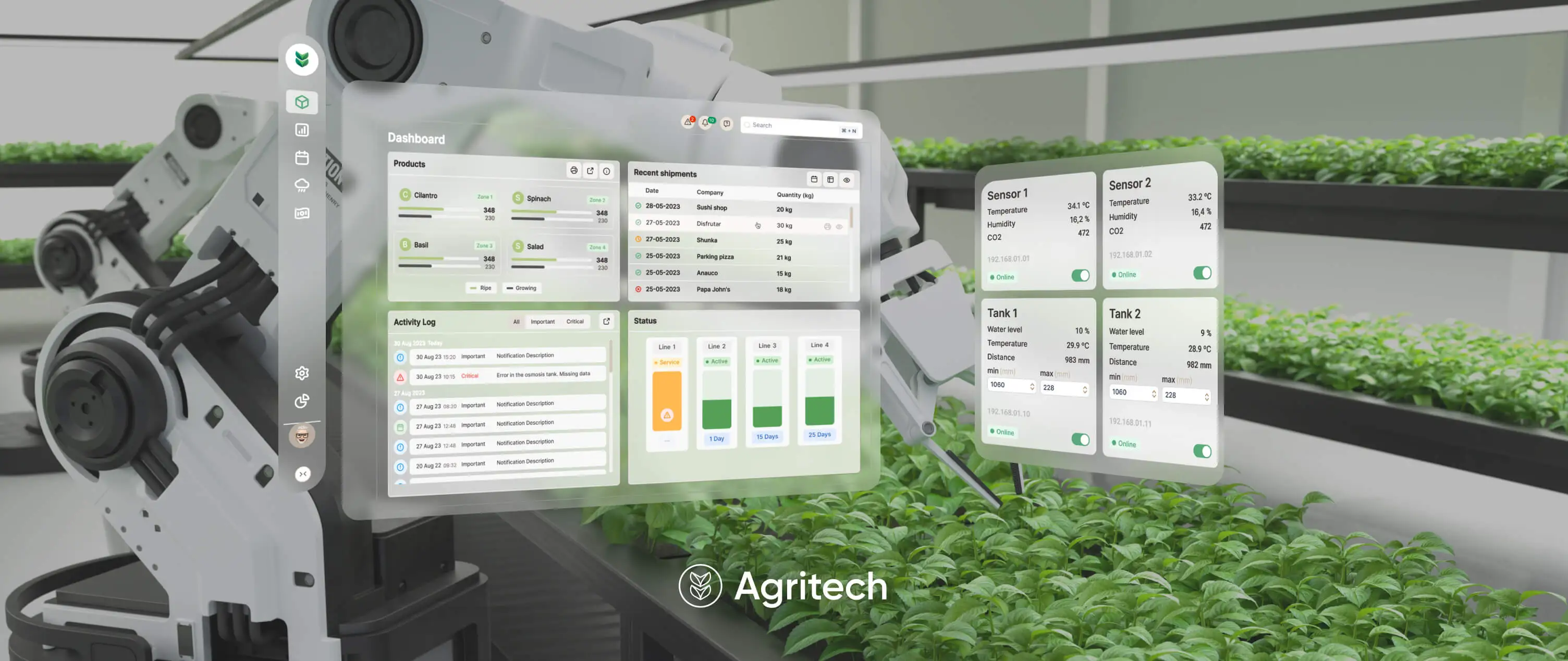
Starting point
A greenhouse business in Western Ukraine specializing in herb cultivation partnered with COAX for a digital transformation. Facing challenges with paper-based documentation and inefficient resource handling, it aimed to shift towards a more effective, sustainable approach to run its 6-hectare facility.
Navigating the complexity of agribusiness operations
The greenhouse faced significant operational challenges. Managing vast volumes of data, from crop yields to resource allocation, was cumbersome using outdated paper records and spreadsheets. This inefficiency hindered the ability to track key performance indicators, analyze historical data, and make informed decisions. The scattered nature of critical information, such as average crop weights, environmental conditions, and resource usage, further compounded the problem.
Moreover, the greenhouse's distant location posed an additional challenge for the owners, who required real-time insights into production and sales without the need to physically visit the site.
From cumbersome to efficient with connected farming
Our software development team, comprising a backend developer, a frontend developer, a UI/UX designer, and a manual QA expert, undertook this project with a clear vision: to create a web application that addresses the multifaceted needs of modern agribusinesses.
In just 6 weeks, COAX’s team transformed an initial concept into a market-ready product featuring a comprehensive financial module. We kicked off the product discovery, exploring the initial concept’s potential. After confirming its viability, our team our team provided a bespoke MVP development services based on a unified architecture. More features were added in the next 4,5 months, evolving into a full-fledged platform that seamlessly integrates various business functions.
- Perception layer: IoT devices across the greenhouse collect environmental data like temperature, humidity, and soil moisture. These sensors converted physical parameters into digital signals for processing.
- Connectivity layer: LPWAN for long-range, low-power communication ensured that all devices within the large greenhouse area remained interconnected and rapidly transmitted data to the cloud-based system.
- Processing layer: The data collected by sensors was aggregated, abstracted, and stored on cloud servers. This layer was crucial for filtering and organizing the vast amounts of data generated by the greenhouse's operations.
- Application layer: A custom web app interprets the processed data, providing actionable insights through dashboards and charts. This enabled the greenhouse management to make data-driven decisions regarding crop health, irrigation, and resource allocation.
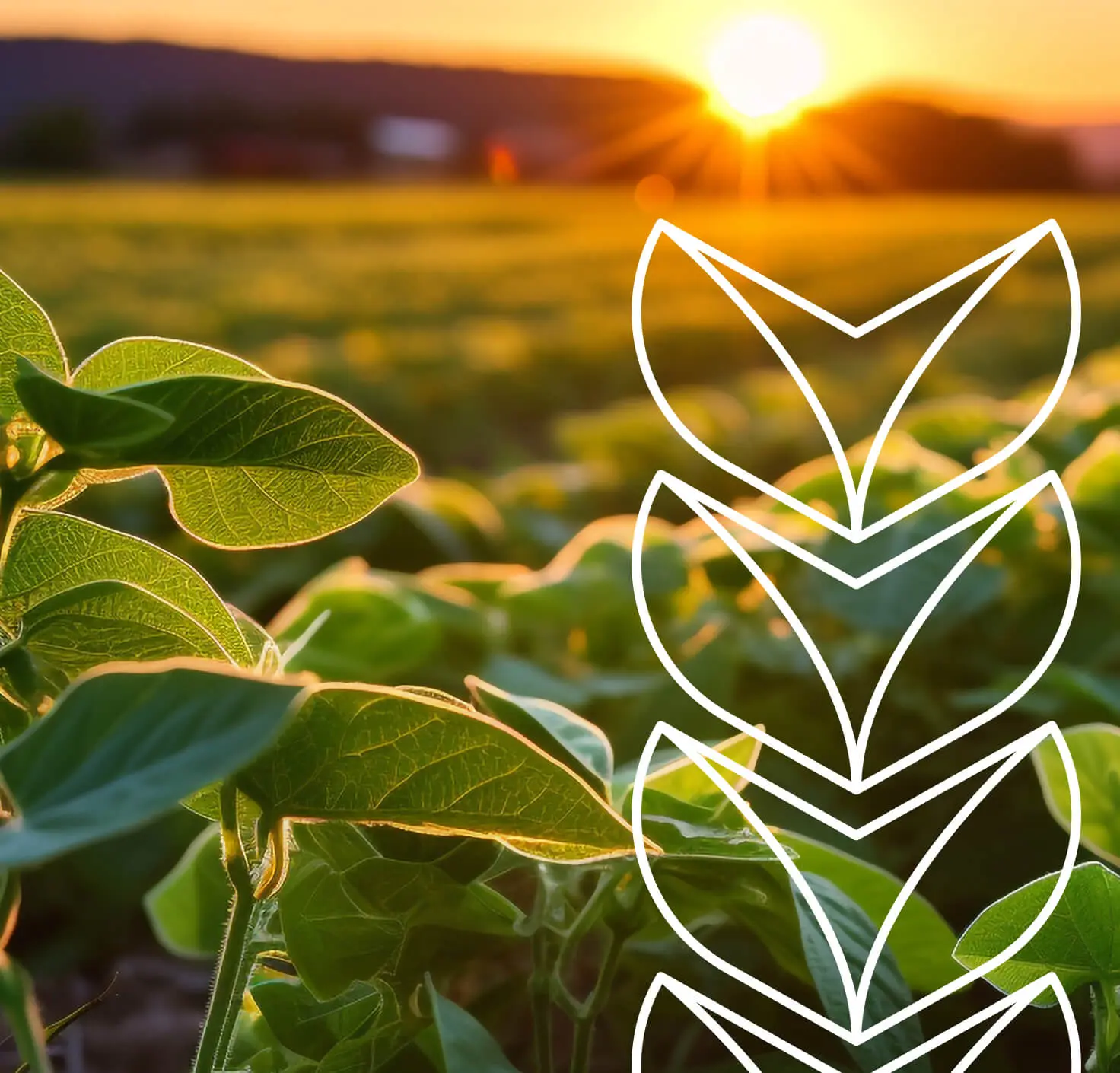
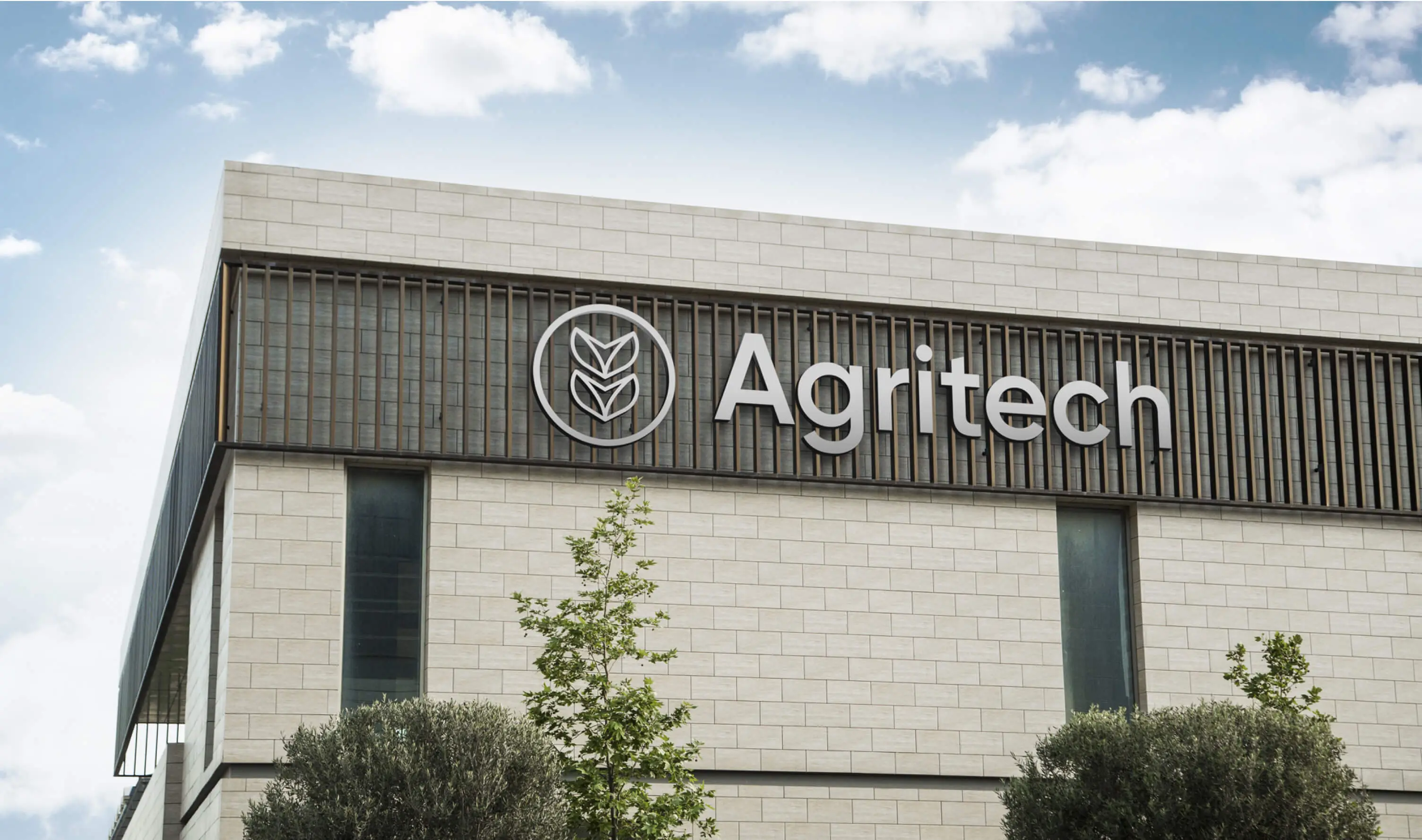
Key features
Production analytics
The platform gathers data from IoT devices and custom hardware APIs, providing real-time analytics on crop stages, volume, temperature, humidity, and resource consumption. 70% of the data is collected automatically, empowering the greenhouse to monitor and optimize its production processes intelligently.
Financial management
Unified accounting workflows, such as tracking invoices, expenses, revenues, and payments, provide a holistic view of the greenhouse's financial health.
Operational control
A user-friendly dashboard offers insights into workforce performance, product output, and expenditure, streamlining strategic decision-making and operational efficiency.
CRM and supplier management
The platform enhances customer and supplier relationships by maintaining detailed records of transactions, average ticket sizes, and procurement costs.
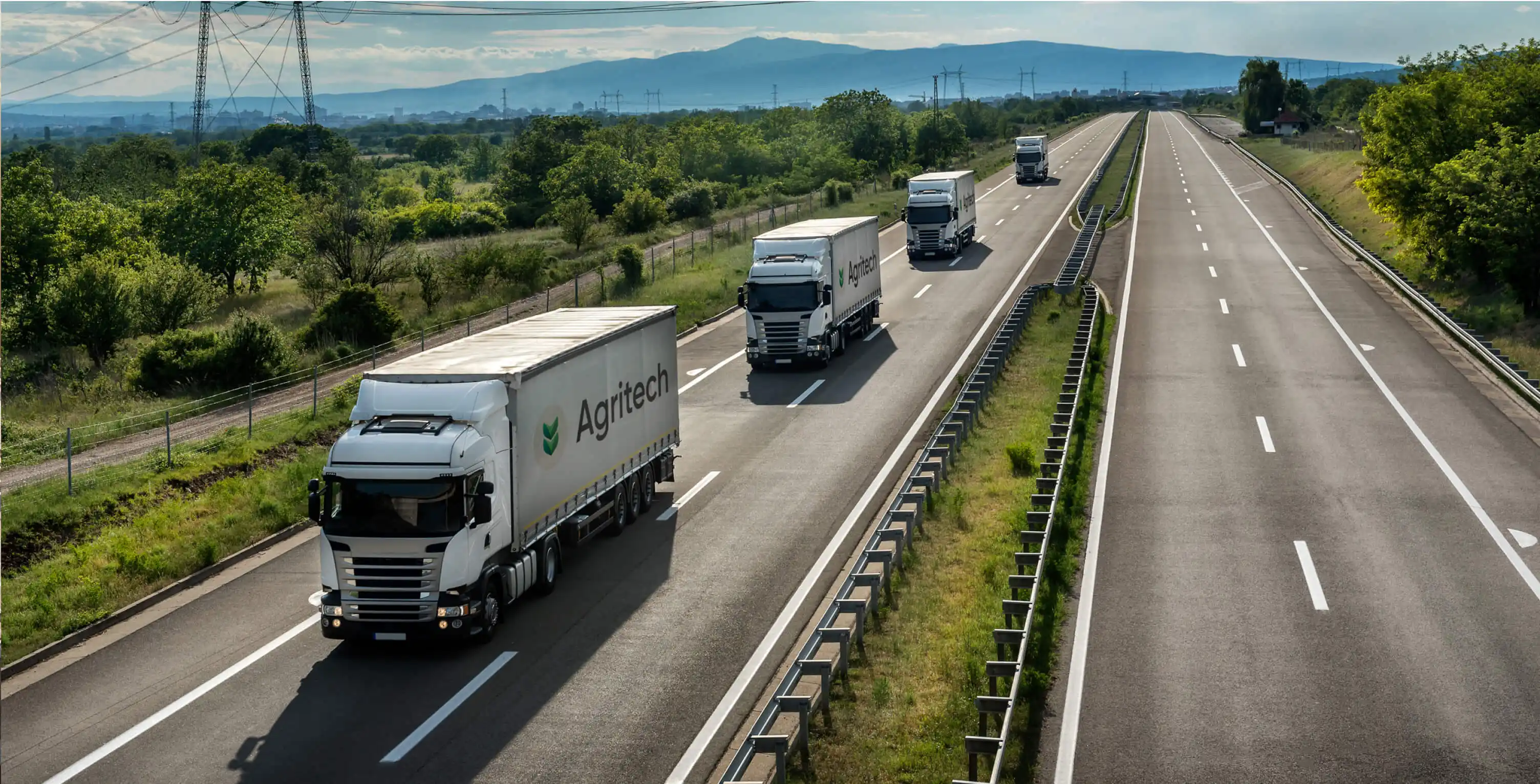
The impact: Cultivating success in agritech
100% transparency
The digitization of operations has made every process transparent, providing real-time visibility and historical data analysis. This boosted decision-making capabilities, enabling the owners to optimize production on the fly.
14% revenue growth
By streamlining operations and optimizing resources, the greenhouse experienced a 14% increase in revenue in 2023.
Resource waste reduced by 25%
Precise monitoring and management of natural resources and workforce helped reduce waste by 25% and lower operational costs by 12%.
15% more yield
Real-time data on environmental conditions and crop health allowed for adjustments that increased yield by 15% and improved crop quality across several parameters.
Remote management capabilities
The owners can monitor and manage the greenhouse remotely, ensuring optimal operation without the need for constant on-site presence.
Agro-tourism
An innovative byproduct of this digital transformation is the launch of an "open greenhouse" for agrotourism. Since September 2023, visitors can engage with and learn about sustainable farming practices firsthand.
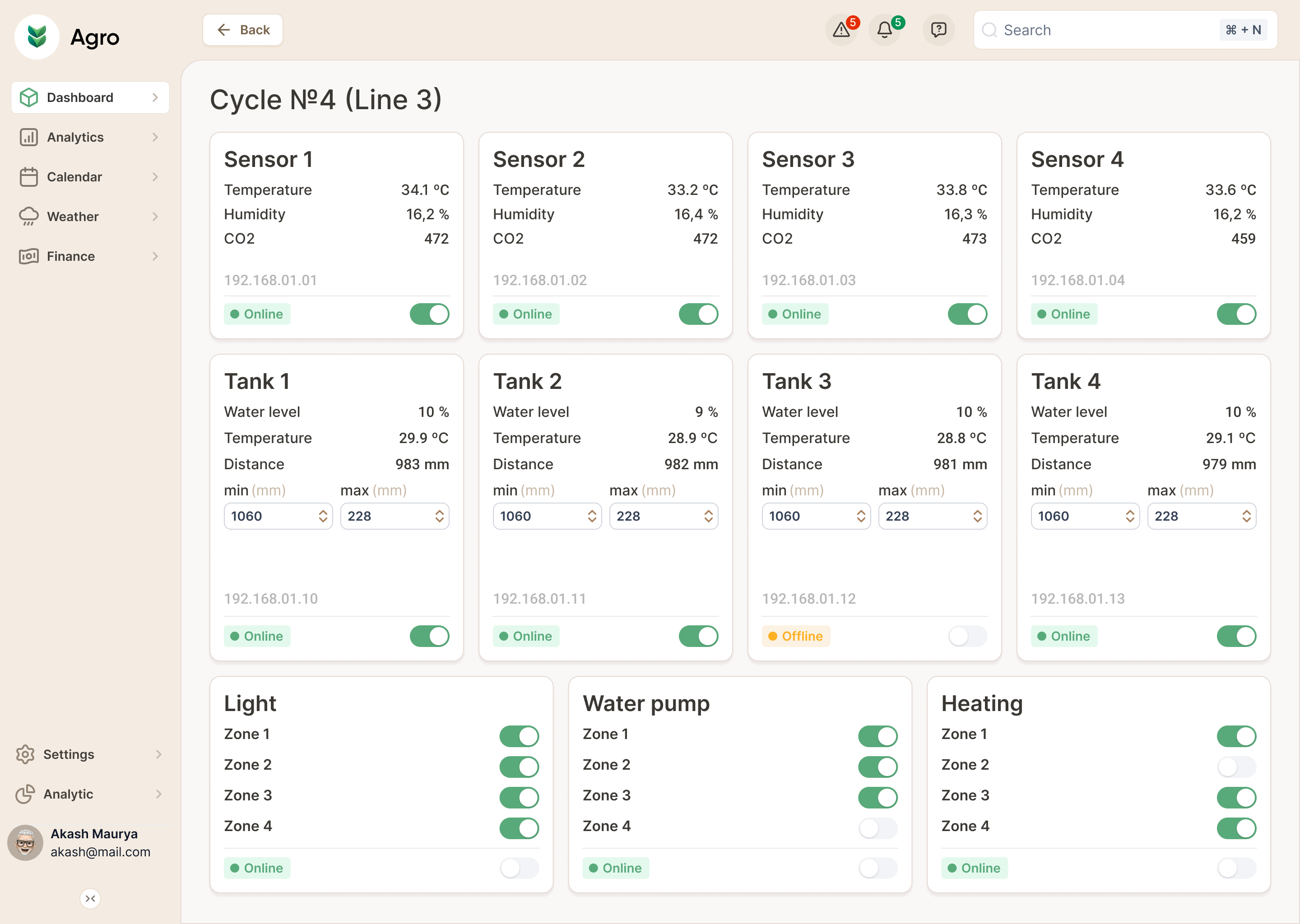
Leading the way in agribusiness innovation
By integrating connected farming technologies, the greenhouse not only improved its operational efficiency and crop yield but also set a precedent for sustainable and smart agriculture in the region.